1. Introduction
The core contents of thermochromic microcapsule are leuco-dye, color developers and temperature controllers. By using different temperature controllers, NCC thermochromic products come in various activation temperatures.
2. Product Description
A. Color Conversion:
When the temperature is raised to a specified temperature, it goes from colored to colorless. The product returns to the original color as the temperature cools down.
Colored as temperatures cool down | ![]() |
![]() |
![]() |
Colorless as temperatures raise |
B. Available Activation Temperatures:
–15℃ ~ 70℃
C. Color:
15 available colors for each activation temperature. (Except 70℃, only black and dark blue available for 70℃) All colors can be mixed with each other or added other pigments.
![]() |
![]() |
![]() |
![]() |
Red
186C |
Rose Red
238C |
Margenta
Rubine Red C |
Brown
497C |
![]() |
![]() |
![]() |
![]() |
Vermilion
185C |
Orange
021C |
Yellow
387C |
Charm Green
Green C |
![]() |
![]() |
![]() |
![]() |
Green
335C |
Sky Blue
313C |
Turkish Blue
320C |
Blue
301U |
![]() |
![]() |
![]() |
|
Dark Blue
294C |
Violet
2728C |
Black
Black 5C2X |
3. Applications
A. Available Products & Applicability
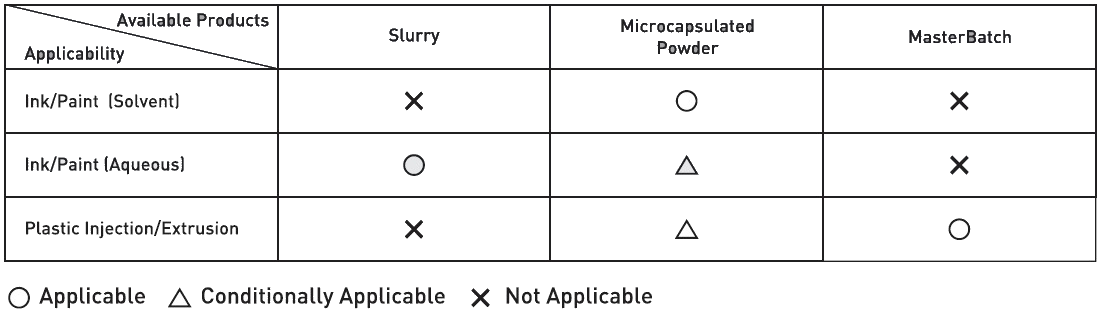
B. Thermochromic Slurry
a. Product Description
Thermochromic slurry is microencapsulated aqueous dispersion with good dispersal in water, suitable for water based ink, paint. It contains 45%(±5%) of solid content. The average particle size of the slurry is 3-10µm.
b. Properties
Good dispersal in water, suitable for aqueous based screen printing, paint, and ink.
c. Recommended Concentrations
For aqueous based ink/paint 5%~60% w/w
(For best results, about 25% concentration is required for 20µm film thickness)
d. General Recommendations
Avoid high polarity solvents, such as methanol, ethanol, acetone and methyl-ethyl-ketone, which will affect the microcapsules contents through permeation.
Slurry may clump together during storage. Heating the slurry to 45℃ in a double boiler to disperse.
Changes of PH may cause changes of color conversion.
C. Thermochromic Microcapsulated Powder
a. Product Description
Consist of compound formulation, containing moisture ≦ 3%. Its average particle size is 3-10µm.
b. Properties
With good solvent resistance and dispersal, thermochromic microencapsulated powder is suitable for ink/paint and plastic injection/extrusion.
c. Recommended Concentrations
For solvent/ aqueous based ink/paint 5%~30% w/w
(For best results, about 25% concentration is required for 20µm film thickness)
For plastic injection/extrusion 0.1% ~5% w/w
(For best results, about 0.5% concentration is required for 0.2cm plastic thickness)
d. General Recommendations
Avoid high polarity solvents, such as methanol, ethanol, acetone, and methyl ethyl ketone, which will affect the microcapsules contents through permeation.
The processing temperatures of plastic applications should not be over 230℃.
D. Thermochromic Masterbatch
a. Product Description
Thermochromic masterbatch contains 12%-18% of microcapsules. The percentage of microcapsules contained depends on its different color formulations.
b. Properties
Dispersed and used easily, can be directly applied to plastic injection/extrusion.
c. Recommended Concentrations
For plastic injection/extrusion 1% ~5% w/w
(For best results, about 0.5% concentration is required for 0.2cm plastic thickness)
d. General Recommendations
Standard masterbatch is PE masterbatch.
Add phenolic heat stabilizers only may destroy the color changing properties.
UV stabilizer/absorbent may affect the color changing properties.
4. Miscellaneous
A. IT&DT chart
Chart of color change to temperatures: Exp. 31℃ Dark Blue.
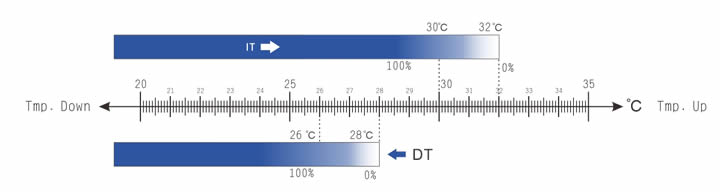
When temperature is going up to 30℃, red color begins fading. The color completely disappears at 32℃.
When temperature is going down to 28℃, red color begins appearing. The color is strongest at 26℃.
Please note each color has its specific activation temperatures. The heat conduction speed of base materials does affect the thermochromic products reactions to temperatures.
B. Multi-Phase Color Change
a. Two-phase Color Change

b. Three-phase Color Change
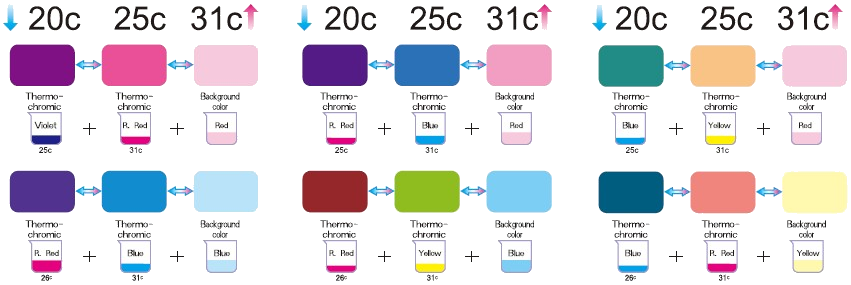
c. Multi-phase Color Change

5. Others
A. Storage: Keep sealed in a dark, cool place, away from direct sunlight.
B. Expiratory date: Half year for Dark Blue, Charm Green, Turkish Blue and Brown from the date of manufacture. Two years for the others.
C. Certifications: EN-71 & RoHS passed. Safe for food grade packing and toys.
1. Introduction
Glow in the dark materials can absorb and store light/heat energy, then glow in the dark. They can be recharged and continue glowing unlimited times as long as they get recharged sufficiently. The materials can be charged faster by exposure to sunlight/UV light.
2. Product Description
A. Color Conversion
Original color in the light | ![]() |
![]() |
![]() |
Glow color in the dark |
B. Color:
Four colors (YC/YA/BA/PA) available for long-lasting glow powder One color (RA) for conventional(Zinc Sulfide) powder
![]() |
![]() |
![]() |
![]() |
![]() |
![]() |
Yellow Green NL-YA
|
Blue NL-BA
|
||||
![]() |
![]() |
![]() |
![]() |
![]() |
![]() |
Purple NL-PA
|
Red NL-RA
|
C. Brightness:
Two items (YA & YC) are available for the yellow-green powder.Glow of YC is brighter than YA. Please refer to www.colorchange.com.tw for afterglow performance of each item.
3. Applications
A. Available Products & Applicability
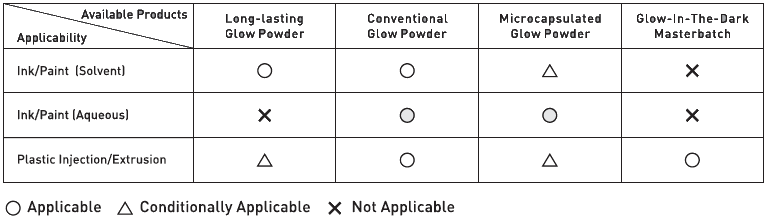
B. Long-lasting Glow Powder (Strontium Aluminates type)
a. Product Description
The density of long-lasting glow powder is 3.6, It’s made of strontium aluminates, which is non-toxic and non-radioactive.
b. Properties
The long-lasting glow powder is pigment, suitable for plastic injection and solvent based ink/paint. Its afterglow time is ten times longer than that of the conventional type. Good weather resistance, applicable to both outdoor and indoor.
c. Recommended Concentrations
For solvent based ink/paint 5%~30% w/w(25%)
(For the best result, about 25% concentration is required for 20um film thickness)
For plastic injection/extrusion 5%~15% w/w(10%)
(For the best result, about 0.5% concentration is required for 0.2cm plastic thickness)
d. General Recommendations
Avoid moisture during processing. 2. Avoid direct contact with metals. 3. Avoid frictions at high temperatures.
Guidelines for applications of paint/screen printing ink:
◎Use neutral or weak alkaline clear resin
◎To avoid precipitates of glow powder occurred in glow paint, use high-viscosity resin and add an anti-precipitation agent to the paint. Stirred well before use. Add thinner if necessary. Do not add any heavy metal compounds.
◎Use white, or light color as a background for the best results. Any color other than white will diminish glow.
◎Use a 80-120 mesh screen for screen printing for the best results.
Guidelines for applications of plastic injection/extrusion:
◎When applying long-lasting glow powder directly to plastic injection/extrusion, it is recommended to add some lubricants to mix well and prevent oxidation.
◎Make the long-lasting glow powder processed in cylinders as short as possible.
◎Use plastic of light-color, fluorescent-color, or transparent-color as the base plastic for the best glow strength.
C. Conventional Glow Powder (Zinc Sulfide type)
a. Product Description
Made by Zinc sulfide, the density of conventional glow powder is 4.1, having shorter afterglow time.
b. Properties
Conventional glow powder is pigment, suitable for plastic injection and solvent /aqueous based ink/paint, having brighter start glow.
c. Recommended Concentrations
For solvent/aqueous based ink/paint 5%~30% w/w(25%)
(For the best result, about 25% concentration is required for 20um film thickness)
For plastic injection/extrusion 5% ~15% w/w(10%)
(For the best result, about 0.5% concentration is required for 0.2cm plastic thickness)
d. General Recommendations
Please refer to long-lasting glow powder for recommendations on paint/screen printing ink applications.
Guidelines for applications of plastic injection/extrusion:
◎Use plastic of light-color, fluorescent-color, or transparent-color as the base plastic for the best glow strength.
D. Microcapsulated Glow Powder
a. Product Description
Encapsulated long-lasting glow powder by polymer can avoid oxidation destroying the glowing properties of the powder, which makes it suitable for aqueous based applications.
b. Properties
Microcapsulated glow powder can be directly applied to aqueous based ink/paint.
c. Recommended Concentrations
For solvent/aqueous based ink/paint 5% ~30% w/w(25%)
(For the best result, about 25% concentration is required for 20um film thickness)
d. General Recommendations
Please refer to conventional glow powder for recommendations on paint/screen printing ink applications.
E. Glow-in-the-Dark Masterbatch
a. Product Description
Glow-in-the-dark masterbatch is made by mixing plastic and long-lasting glow powder, which can prevent glow powder turning dark due to oxidization when applied to plastic injection/extrusion.
b. Properties
Dispersed and used easily, can be directly applied to plastic injection/extrusion.
c. Recommended Concentrations
For plastic injection/extrusion 5% ~15% w/w
(For best results, about 10% concentration is required for 0.2cm plastic thickness)
d. General Recommendations
Use plastic in light colors, fluorescent colors, or transparent color as base plastic for the best glow strength.
4. Miscellaneous
A. Particle analyses: type 1 is finer pass 100 mesh, type 2 is finer pass 150 mesh, type 3 is finer pass 200 mesh, and type 4 is finer pass 300 mesh.
B. Fluorescent agents, dye, or pigments can be added to the glow powder to adjust its before glow/afterglow colors. The powder can also be mixed to each other to get the glow color desired. Too many pigments added may diminish glow.
5. Others
A. Storage: Keep sealed in a dry and cool place. Do not use metal containers. Moisture in the air will shorten its shelf life and destroy glow properties. Best within two years if stored correctly.
B. Certifications: EN-71 & RoHS passed. Safe for food grade packing and toys.